
CNC Grinding Minnesota

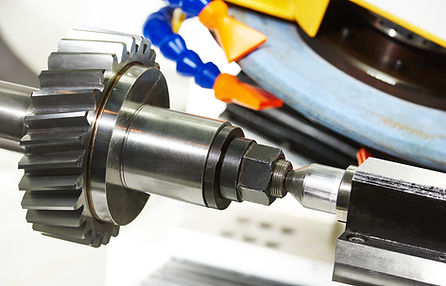
A very effective way to manufacture hard-to-machine parts from raw material stock is to use a new form-and-finish operation known as CNC cylindrical creep-feed grinding. Traditional cylindrical grinding is used to remove material in thousandths or tenths of a thousandth of an inch per pass. CNC cylindrical creep-feed grinding, on the other hand, can be used to remove up to 1/3" or more of stock in one rough and one finish pass, during a work rotation lasting a minute or longer. Creep-feed is a technique not previously used in cylindrical grinding.
However, with a sufficiently rigid and accurate machine tool and with the proper application of wheels, wheel conditioning, coolant and grinding techniques, cylindrical creep-feed grinding can be extremely effective. In cases where very high production rates are required, or very difficult-to- grind materials are encountered, continuous dressing can be applied to the creepfeed grinding wheel to assure quality with substantial productivity increases.
Cross-bred from its cylindrical grinding distant cousin and the now accepted technique of flat surface creepfeed grinding allows for the efficient high quality grinding of round and nonround parts, including punches, rotary dies, cams, and polygons. Even intricate forms such as medical prostheses or vane segments for jet engines can be cylindrical creep-feed manufactured from round blanks, users of this technology are discovering. In CNC cylindrical creep-feed grinding, the depth of cut (DOC) can be as much as 0.300" or more in one pass, depending on material hardness and form depth. Peripheral feed rates are typically 1" to 10" per minute. A second pass is usually performed for the desired surface finish, and size tolerance to 0.0002". On nonround parts using the technique of radial contouring, the rate of stock removal frequently varies.
The work spindle is critical. It has to be very stiff, and backlash designed, and equipped with heavy preloaded bearings, especially for nonround parts, where after contouring and better repeatability are needed. Other requirements are a high-velocity coolant, a porous structured grinding wheel, effective wheel truing and dressing, and an efficient method of swarf removal.
These benefits can significantly outweigh the high wheel consumption associated with continuous dressing creepfeed (CDCF). While the cost for wheels may increase by 25 to 50 percent, overall process control is much improved, and softer wheels that are continuously dressed keep stress on the workpiece to a minimum. These and other advantages can increase output, eliminate additional machines, and provide superior part quality. Successful CNC cylindrical creepfeed grinding demands a rugged and very rigid grinding machine of from 15 to 50 horsepower. Constant surface speed must be provided by the wheel spindle unit. CNC cylindrical creep-feed grinding users can also benefit from the elimination of multiple primary operations, reduced handling and setup, comparatively low tooling costs, an enhanced capability to operate on a just-in-time basis, and reduced space needs on the shop floor.